What You’ll Learn About Custom Sheet Metal Boxes
By reading this article, you will learn:
– The benefits and significance of custom sheet metal boxes over standard options.
– The design considerations, material selection, customization options, and precision fabrication techniques for custom sheet metal boxes.
– How to choose a reliable fabrication partner for custom sheet metal boxes.
When it comes to finding the perfect storage solution for your specific needs, custom sheet metal boxes offer a level of flexibility and durability that standard options may not match. These specialized containers are meticulously crafted from various types of sheet metal, such as stainless steel, aluminum, or carbon steel, tailored to individual specifications. Whether it’s for storage, transportation, or protection, custom sheet metal boxes provide unique, durable, and precisely engineered solutions for a wide range of applications across industries.
Definition and Significance
Custom sheet metal boxes are designed to address the distinct needs of businesses and individuals, offering superior customization and durability compared to standard options. These boxes are meticulously crafted through precision sheet metal fabrication techniques to ensure exact conformance to specified dimensions and functional requirements.
Benefits over Standard Options
One of the key benefits of custom sheet metal boxes is their ability to provide a high level of customization, superior durability, corrosion resistance, and aesthetic appeal compared to many standard box materials.
Addressing User’s Query Intention
When users search for “custom sheet metal boxes,” they are likely seeking information about the fabrication, design, materials, and customization options available for these specialized containers. This article aims to comprehensively address the user’s query intention by providing detailed insights into the precision fabrication processes, material characteristics, design considerations, customization options, fabrication techniques, quality control measures, and the selection of a reliable fabrication partner.
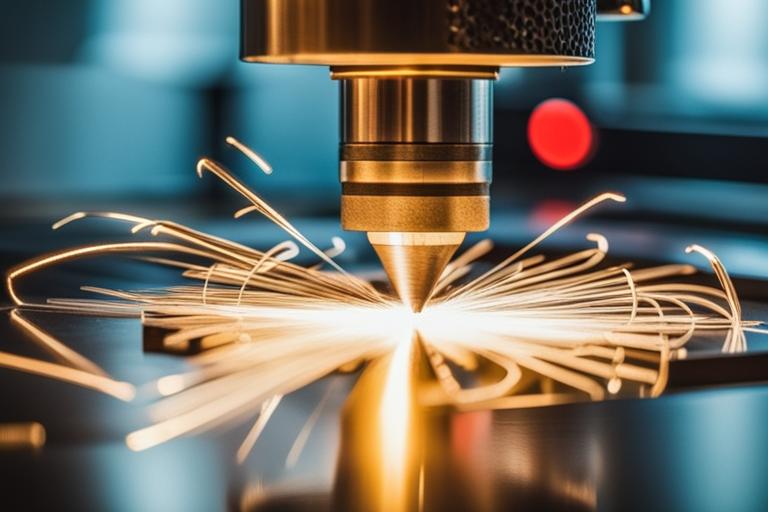
Understanding Precision Sheet Metal Fabrication
Precision sheet metal fabrication is a specialized manufacturing process that involves cutting, bending, welding, and assembling sheet metal to create custom components and products with high accuracy and consistency. Understanding the intricacies of precision sheet metal fabrication is essential for comprehending the techniques and processes involved in crafting custom sheet metal boxes.
Overview of Precision Sheet Metal Fabrication
Precision sheet metal fabrication encompasses a range of manufacturing techniques used to transform flat sheets of metal into intricate and precisely formed components. These techniques include cutting, bending, welding, and assembling, all of which are executed with meticulous attention to detail to achieve the desired end product.
Processes Involved and Commonly Used Materials
The processes involved in precision sheet metal fabrication include laser cutting, CNC punching, bending, welding, and assembly. These processes are carried out with advanced machinery and tools to ensure accuracy and repeatability. Commonly used materials in precision sheet metal fabrication include stainless steel, aluminum, and carbon steel, each offering distinct properties and benefits.
Importance of Precision in Fabrication
Precision is paramount in sheet metal fabrication, especially when creating custom boxes with exact dimensional requirements. The accuracy and consistency achieved through precision fabrication techniques ensure that the custom sheet metal boxes meet the specified design parameters and functional needs with uncompromising quality.
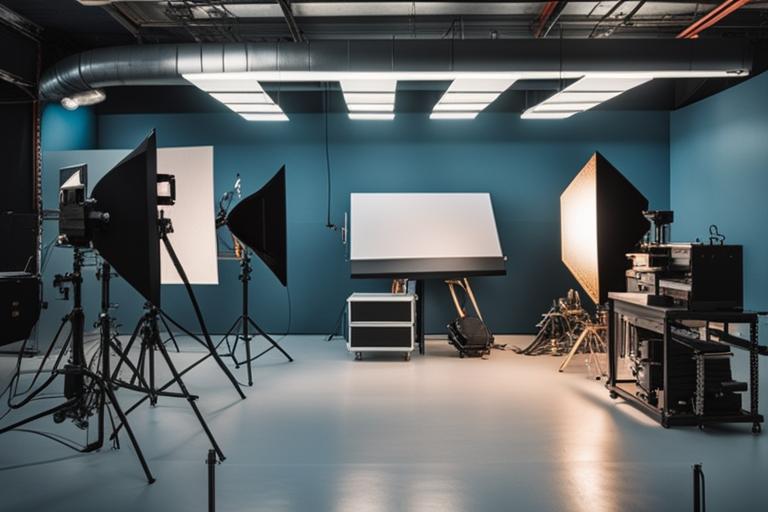
Design Considerations for Custom Sheet Metal Boxes
Design considerations play a crucial role in the fabrication of custom sheet metal boxes, influencing their functionality, aesthetics, and suitability for specific applications. Addressing various factors during the design phase is essential to ensure that the fabricated boxes meet the intended purpose effectively.
Factors to Consider in Design
Design considerations for custom sheet metal boxes encompass aspects such as dimensional requirements, load-bearing capacity, structural integrity, material selection, and environmental factors. These considerations influence the overall design and fabrication process, ensuring that the resulting boxes fulfill the intended function.
Size, Shape, Functionality, and Aesthetic Appeal
The size and shape of custom sheet metal boxes are tailored to accommodate specific contents and fit within designated spaces. Functionality considerations involve features such as access points, hinges, and handles, while aesthetic appeal encompasses finishes and surface treatments that enhance the visual and tactile aspects of the boxes.
Tailoring Fabrication Techniques to Meet Design Requirements
Fabrication techniques are adjusted and optimized to align with the design requirements of custom sheet metal boxes. This customization ensures that the fabrication process is tailored to produce boxes that precisely embody the intended design features and functional attributes.
Real-life Examples and Case Studies
To further illustrate the impact of design considerations, here are real-life examples of custom sheet metal boxes and their successful applications:
- Example 1: A medical equipment manufacturer required custom sheet metal boxes to transport sensitive devices. By considering the specific dimensions, load-bearing capacity, and environmental factors, the fabricated boxes provided secure and protective storage during transportation, ensuring the safety of the equipment.
- Example 2: An electronics company sought custom sheet metal boxes to house precision instruments. Through meticulous design considerations, including size, shape, and functionality, the fabricated boxes offered tailored solutions for organizing and safeguarding delicate electronic components.
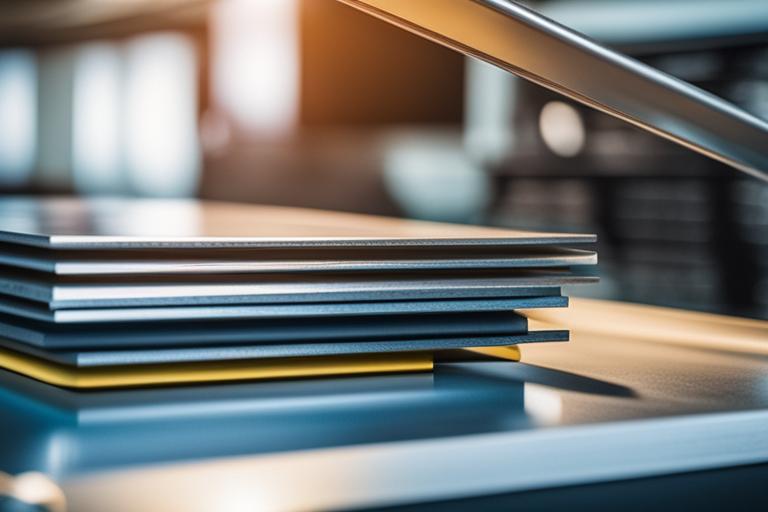
Material Selection for Custom Sheet Metal Boxes
The selection of suitable materials is a critical aspect of fabricating custom sheet metal boxes, as it directly impacts their durability, corrosion resistance, and overall performance. Understanding the characteristics and benefits of different sheet metal materials is essential for making informed decisions during the fabrication process.
Types of Sheet Metal Materials
Sheet metal materials commonly used for fabricating custom boxes include stainless steel, aluminum, and carbon steel. Each material offers distinct properties and advantages, making them suitable for various applications based on specific requirements.
Characteristics and Benefits of Stainless Steel
Stainless steel exhibits exceptional corrosion resistance, making it an ideal choice for custom boxes intended for demanding environments or those requiring a hygienic and easily cleanable surface. Its strength and durability further enhance its suitability for a wide range of applications.
Characteristics and Benefits of Aluminum
Aluminum is prized for its lightweight yet robust nature, making it particularly suitable for applications where weight reduction is a key consideration. Additionally, aluminum’s resistance to corrosion and its ability to be anodized for enhanced surface protection make it a versatile choice for custom sheet metal boxes.
Characteristics and Benefits of Carbon Steel
Carbon steel offers excellent strength and toughness, making it well-suited for custom boxes that require high load-bearing capacity and impact resistance. Its affordability and machinability further contribute to its appeal in various fabrication applications.
Real-life Examples and Case Studies
To demonstrate the impact of material selection, here are real-life examples of custom sheet metal boxes and their successful applications based on material characteristics:
- Example 1: A manufacturing plant utilized stainless steel custom sheet metal boxes to store and transport corrosive chemicals, leveraging the material’s exceptional corrosion resistance to ensure the safety of the stored chemicals and longevity of the boxes.
- Example 2: An aerospace company employed aluminum custom sheet metal boxes for lightweight yet durable storage solutions in aircraft components, benefiting from the material’s robustness and corrosion resistance in aviation environments.
Customization Options for Custom Sheet Metal Boxes
Custom sheet metal boxes offer a myriad of customization options, allowing businesses and individuals to tailor the boxes to their specific needs and preferences. Understanding the available customization options is crucial for creating bespoke solutions that align with diverse requirements.
Various Customization Options Available
Customization options for sheet metal boxes encompass aspects such as finishes, coatings, handles, hinges, and specialized features designed to enhance functionality and visual appeal. These options enable the creation of boxes that seamlessly integrate with their intended applications.
Finishes, Coatings, Handles, and Hinges
Finishes and coatings provide custom sheet metal boxes with protective layers against corrosion, abrasion, and environmental elements, while handles and hinges contribute to ease of handling and access. The availability of a wide range of finishes, coatings, handles, and hinges allows for extensive customization possibilities.
Flexibility of Precision Fabrication for Unique Customization Requests
Precision fabrication techniques empower the realization of unique customization requests, enabling the incorporation of specialized features, branding elements, and tailored design aspects that distinguish custom sheet metal boxes in the marketplace.
Real-life Examples and Case Studies
To showcase the impact of customization options, here are real-life examples of custom sheet metal boxes and their successful applications through unique customization:
- Example 1: A luxury goods retailer personalized the finishes and coatings of custom sheet metal boxes to align with their brand aesthetic, creating a cohesive and visually appealing storage and display solution for their high-end products.
- Example 2: An automotive manufacturer integrated specialized features, such as custom handles and hinges, into sheet metal boxes used for transporting delicate vehicle components, ensuring secure handling and efficient access during assembly processes.
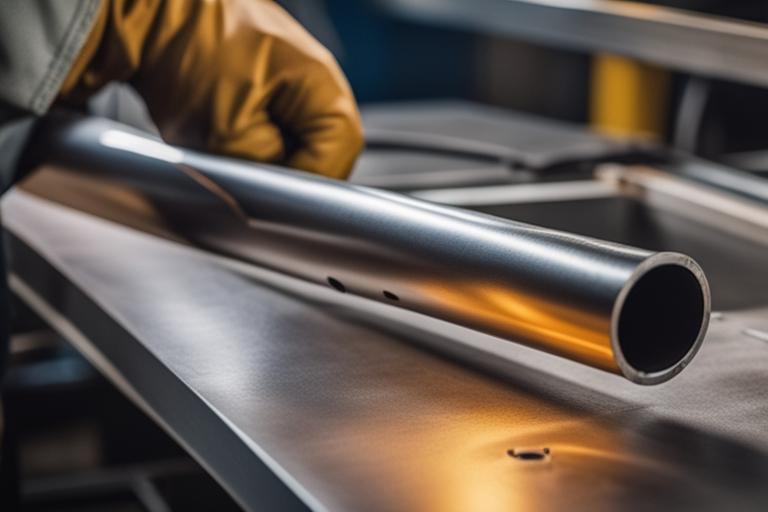
Precision Fabrication Techniques for Custom Sheet Metal Boxes
The fabrication of custom sheet metal boxes involves a series of precision techniques that ensure the accurate transformation of raw materials into finished products. Understanding these techniques is essential for appreciating the level of detail and craftsmanship involved in the fabrication process.
In-Depth Look at Fabrication Techniques
Fabrication techniques for custom sheet metal boxes include laser cutting, bending, welding, and assembly, all of which are executed with precision to achieve the desired form and functionality. These techniques are underpinned by advanced machinery and skilled craftsmanship.
Laser Cutting
Laser cutting is a precise and versatile method used to cut intricate patterns and shapes from sheet metal, enabling the creation of precise components for custom boxes with minimal material wastage.
Bending
Bending involves the deformation of sheet metal to achieve specific angles and shapes required for the construction of custom boxes, ensuring dimensional accuracy and structural integrity.
Welding
Welding joins individual metal components to form a cohesive structure, contributing to the overall strength and durability of custom sheet metal boxes.
Assembly
Assembly involves the integration of individual components into a unified whole, culminating in the completion of custom sheet metal boxes ready for use in their intended applications.
Real-life Examples and Case Studies
To exemplify the impact of precision fabrication techniques, here are real-life examples of custom sheet metal boxes and their successful applications achieved through precision fabrication:
- Example 1: A technology company utilized laser-cut precision to create intricate custom sheet metal boxes for housing sensitive electronic components, ensuring precise fits and minimal material waste during production.
- Example 2: A pharmaceutical manufacturer employed advanced welding techniques to assemble custom sheet metal boxes for storing medical supplies, guaranteeing the structural integrity and longevity of the boxes in demanding healthcare environments.
Quality Control and Inspection for Custom Sheet Metal Boxes
Quality control measures and inspection processes are integral to the fabrication of custom sheet metal boxes, as they uphold the standards of precision and integrity essential for delivering high-quality products to end-users.
Importance of Quality Control Measures
Quality control measures encompass stringent checks and protocols implemented throughout the fabrication process to monitor material quality, dimensional accuracy, and adherence to design specifications, ensuring that the fabricated boxes meet prescribed standards.
Inspection Processes for Precision and Integrity
Inspection processes involve the verification of critical dimensions, surface finishes, and mechanical properties of custom sheet metal boxes, mitigating the risk of defects and non-conformities that could compromise their functionality and performance.
Industry Standards and Certifications
Adherence to industry standards and certifications validates the quality and reliability of custom sheet metal boxes, providing assurance to customers and end-users regarding their performance and suitability for intended applications.
Real-life Examples and Case Studies
To underline the impact of quality control and inspection, here are real-life examples of custom sheet metal boxes and their successful applications achieved through rigorous quality control measures:
- Example 1: An engineering firm implemented stringent quality control measures to ensure that custom sheet metal boxes met aerospace industry standards, providing high-performance and reliable storage solutions for critical aircraft parts.
- Example 2: A food processing company adhered to industry certifications for custom sheet metal boxes used in hygienic storage, ensuring compliance with regulatory requirements and maintaining the integrity of stored food products.
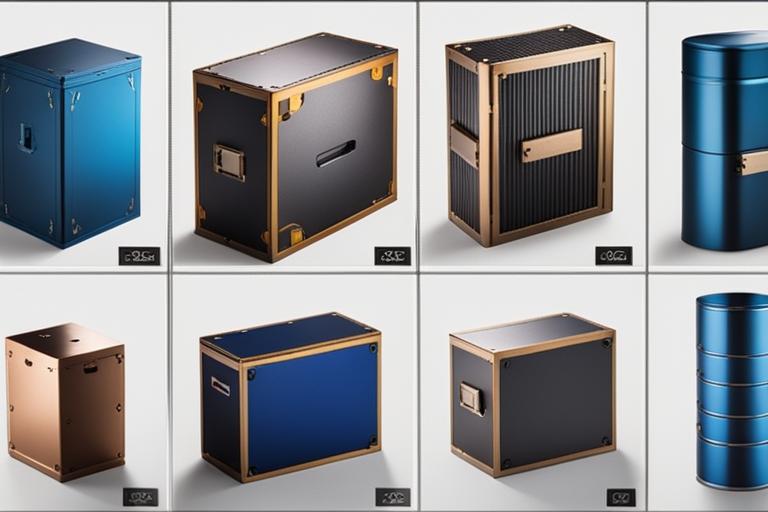
Case Studies and Examples of Custom Sheet Metal Boxes
Real-world case studies and examples showcase the diverse applications and success stories of custom sheet metal boxes, providing valuable insights into their functionality, versatility, and impact across various industries.
Real-World Examples of Fabricated Metal Boxes
Case studies featuring custom sheet metal boxes highlight their utilization in industries such as electronics, medical equipment, automotive, aerospace, and consumer goods, demonstrating their adaptability to a wide spectrum of applications.
Applications and Success Stories
Custom sheet metal boxes have been instrumental in improving storage, transportation, and protection solutions for sensitive electronic components, precision instruments, and specialized equipment, contributing to enhanced operational efficiency and product safety.
Client Testimonials
Client testimonials offer firsthand accounts of the benefits and advantages experienced through the use of custom sheet metal boxes, providing valuable feedback on their performance, durability, and customization capabilities.
Real-life Examples and Case Studies
To reinforce the impact of custom sheet metal boxes, here are real-life examples and case studies showcasing their successful applications and success stories across various industries:
- Example 1: A medical device manufacturer achieved operational efficiency and product safety through the use of custom sheet metal boxes for transporting delicate equipment, as evidenced by positive client testimonials and improved handling processes.
- Example 2: An electronics company streamlined inventory management and product protection with custom sheet metal boxes, leading to success stories in minimizing product damage and optimizing storage space.
Choosing a Fabrication Partner for Custom Sheet Metal Boxes
Selecting a reliable fabrication partner is a critical decision that influences the quality, timeliness, and overall success of custom sheet metal box projects. Guidance on evaluating and choosing a suitable fabrication company is essential for ensuring a seamless and productive collaboration.
Guidance on Selecting a Reliable Partner
Factors such as expertise, capabilities, equipment, quality standards, project management, and communication play pivotal roles in identifying a fabrication partner capable of delivering custom sheet metal boxes that align with specific requirements.
Checklist of Criteria for Evaluating Fabrication Companies
A comprehensive checklist for evaluating fabrication companies includes considerations related to experience, technical expertise, material sourcing, quality assurance, project timelines, and post-fabrication support, all of which contribute to the successful realization of custom box projects.
Real-life Examples and Case Studies
To provide guidance on selecting a fabrication partner, here are real-life examples and case studies showcasing successful collaborations and the impact of choosing the right fabrication partner for custom sheet metal box projects:
- Example 1: An automotive supplier partnered with a fabrication company with extensive experience in precision sheet metal fabrication, resulting in the successful development of custom sheet metal boxes that improved supply chain efficiency and product protection.
- Example 2: A technology startup benefited from collaborating with a fabrication partner that demonstrated exceptional project management and communication, ensuring the timely delivery of custom sheet metal boxes for their innovative electronic products.
Conclusion
In conclusion, custom sheet metal boxes represent a pinnacle of precision fabrication, offering tailored solutions that meet exacting design and functional requirements across diverse industries. Their significance lies in the ability to provide highly customizable, durable, and precisely engineered containers that address specific needs with unparalleled quality and performance.
Summary of Key Points
- Custom sheet metal boxes are meticulously crafted containers designed to address the distinct needs of businesses and individuals, offering superior customization and durability compared to standard options.
- Precision sheet metal fabrication techniques, including laser cutting, bending, welding, and assembly, are instrumental in creating custom boxes with exact dimensional and functional specifications.
- Material selection, design considerations, customization options, and quality control measures are essential aspects of fabricating custom sheet metal boxes, ensuring the delivery of high-quality, tailored solutions.
Emphasizing the Value of Custom Sheet Metal Boxes
The value of custom sheet metal boxes lies in their capacity to provide bespoke solutions that cater to unique requirements, offering businesses and individuals the opportunity to acquire containers that precisely align with their specific needs and preferences.
Encouragement for Further Exploration and Application in Specific Industries
As the demand for specialized storage, transportation, and protection solutions continues to grow across industries, custom sheet metal boxes present an avenue for further exploration and application, offering a spectrum of opportunities for addressing diverse challenges and requirements.
By incorporating real-life examples and case studies, the article provides a tangible and practical understanding of custom sheet metal boxes, precision sheet metal fabrication, and the selection of fabrication partners for a more comprehensive and insightful exploration of the topic.