Threading in sheet metal fabrication is crucial for secure and reliable assembly. Traditional methods like captive fasteners are effective but require time-consuming secondary operations. At Atlas Manufacturing, we’re advancing efficiency with our extrude and tap process, which integrates threading directly into the fabrication workflow. Let’s dive into how this process delivers precision, speed, and cost savings.
Threading Methods in Focus
Captive Fasteners
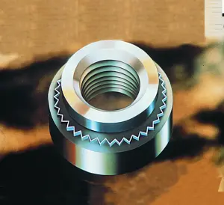

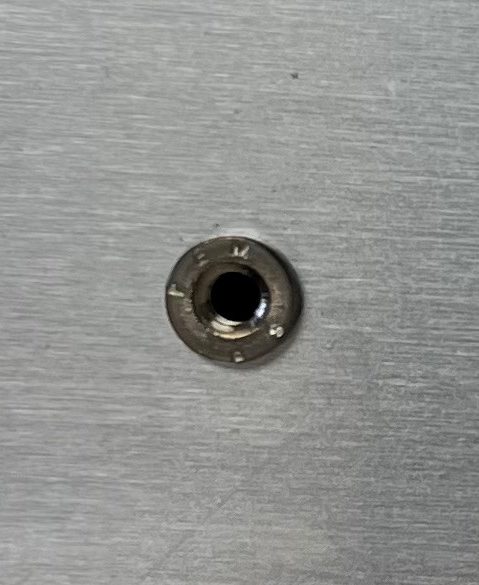
Captive fasteners involve embedding nuts or studs into sheet metal using hydraulic insertion machines. While these connections are durable, the process requires additional handling, increasing time and costs.
Extrude and Tap Process
A more efficient alternative is the extrude and tap process, which eliminates the need for additional hardware. This process forms threads directly into the material using a punch press. Here’s how it works:
- A pilot hole is punched and extruded to form a barrel shape.
- The material is tapped with high-speed tooling (3–6 rotations per second), forming robust, precision threads in a single operation.
Atlas uses Trumpf punching technology, renowned for its speed, precision, and advanced tooling systems.
Atlas’ Extrude and Tap Capabilities:
English Thread Sizes
Size | Pre-pierce Dia. (inches) | Size Category |
---|---|---|
4-40 | 0.1024 | 1 |
6-32 | 0.1260 | 1 |
8-32 | 0.1496 | 1 |
10-24 | 0.1772 | 1 |
1/4-20 | 0.2250 | 2 |
5/16-18 | 0.2850 | 2 |
Metric Thread Sizes
Size | Pre-pierce Dia. (mm) | Size Category |
---|---|---|
M-3 x 0.5 | 0.110 | 1 |
M-3 x 0.5 Form Down | 0.110 | 1 |
M-4 x 0.7 | 0.146 | 1 |
M-5 x 0.8 | 0.183 | 1 |
M-6 x 1.0 | 0.219 | 2 |
M-8 x 1.25 | 0.293 | 2 |
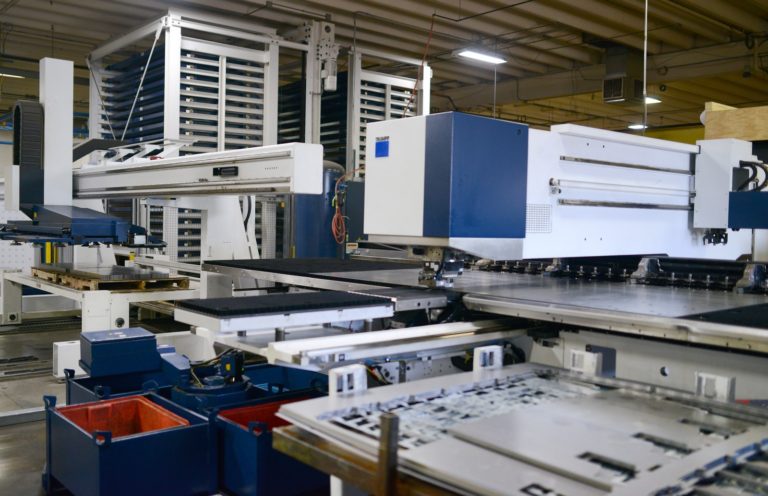
Why Extrude and Tap?
Atlas’s extrude and tap process stands out for its combination of efficiency and precision. Leveraging Trumpf punching technology, the process eliminates the need for secondary threading operations while maintaining the integrity of the sheet metal.
- Efficiency: Combines extrusion and tapping into one seamless operation, reducing production time and labor costs.
- Precision: Advanced Trumpf tools ensure threads are consistent, minimizing errors and waste.
- Surface Integrity: The active die technology and brush tables built into Trumpf machines minimize scratches or marring on the surrounding sheet metal, eliminating the need for additional finishing.
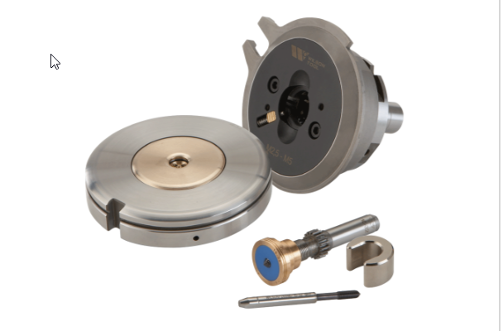
Applications in HPC and Industrial Assemblies
Atlas specializes in providing advanced threading solutions for high-performance compute (HPC) systems and industrial assemblies, where precision, reliability, and efficiency are essential. Our extrude and tap process allows us to meet the stringent demands of these industries, delivering threaded parts that integrate seamlessly into larger assemblies.
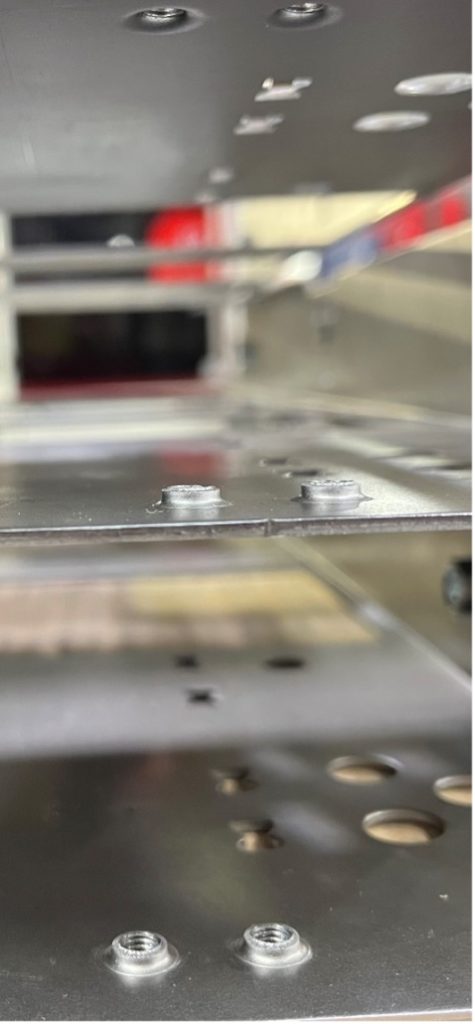
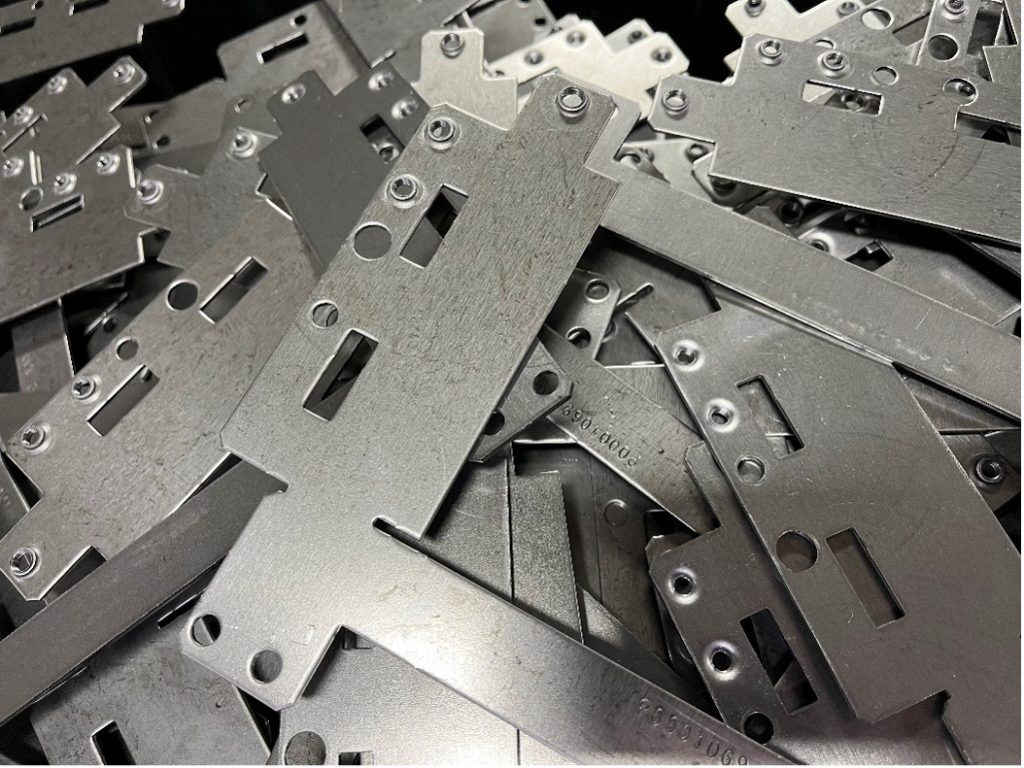
Explore More with Atlas Tech Talks
At Atlas Manufacturing, we pride ourselves on driving innovation in sheet metal fabrication. Stay tuned for more Tech Talks, where we’ll explore cutting-edge processes like laser welding and automated hardware insertion.
Contact us today to learn how we can enhance your next project.