Atlas Manufacturing announces the launch of the MAXFORM hydraulic press brake from Cincinnati Incorporated. The MAXFORM combines state-of-the-art forming speeds and part processing productivity with “smart” controls that speed and simplify programming, setup and part-handling. MAXFORM’s industrial PC-based touch screen control and Windows® software eliminate two-thirds of the programming steps with conventional CNC controls, while advanced hydraulics and control technologies deliver cycle-eating ram speeds — up to 700 ipm — for more strokes per hour and parts per shift.
Exceptional ±0.0002″(3 Sigma) repeatability delivers outstanding consistency for bending of complex parts without deviation, drift or error stacking.
Simulation software enables easy offline part programming, while advanced “see and do” 3D graphics and automatic processing intelligence compensate for varied operator experience levels. A Bend Simulation Module, allows programs to be quickly created offline or at the machine and proved out step-by-step in realistic 3D views to avoid trial bending. Smart controls automatically calculate and apply adjustments for ram reversal position, bottom bending tonnage, gage allowances, and material spring back.
The 6-axis LT backgage provides 3000 ipm repositioning speeds in X and Z axes for fastest sequential bending of complex parts. The high-speed positioning eliminates reset waiting time for more strokes per hour and parts per shift.
The MAXFORM comes with bolt-on Cincinnati Quick Clamp ram nose designed for hardened, sectionalized American tooling. It maximizes ram protection by doubling load capacity from 15 to 30 tons per square inch. The versatile press brake offers Wilson’s Power Express™ hydraulic clamping and a Euro-style Ram Nose for European punch holders.
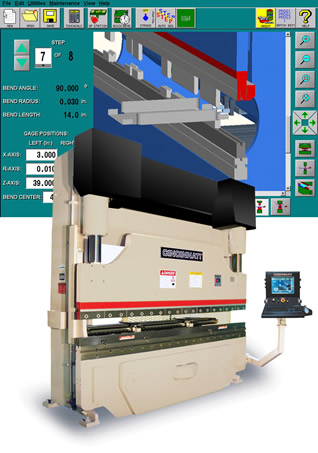