Welcome to Atlas Tech Talks, a series dedicated to sharing insights, best practices, and technical know-how from the world of sheet metal fabrication. In each post, we dive into specific techniques and considerations that help achieve the highest quality in metal processing. Today’s topic explores edge protection for galvanized sheet steel—a crucial factor in industries that rely on corrosion-resistant metal components, like computer chassis and electronics enclosures.
In this article, we’ll discuss best practices for processing galvanized sheet steel, examining how different methods impact edge quality and corrosion resistance. From laser cutting to punching and deburring, we’ll explore which processes provide the best protection for exposed edges. If you have suggestions for future Atlas Tech Talks, we’d love to hear from you! Let us know which topics you’d like us to cover next, as we continue to share knowledge from our team’s expertise.
Introduction
In this edition of Atlas Tech Talks, we delve into the nuances of edge control in galvanized sheet steel processing—a key consideration in fabricating durable, corrosion-resistant components for computer enclosures and electronics. Choosing the right processing method can have a significant impact on edge quality and resistance to oxidation. In this article, we’ll walk through best practices for edge protection, explain the importance of zinc coating, and explore the benefits of punching, shearing, and deburring techniques for galvanized steel.
Understanding Galvanized Sheet Steel and Zinc Coatings
Galvanized sheet steel is widely used in thin sheet metal applications for its corrosion resistance, achieved by applying a zinc coating. This coating is measured in ounces per square foot and is typically categorized as G30 to G90:
• G30 indicates a 0.3 oz/sq ft zinc coating.
• G90 provides a thicker 0.9 oz/sq ft coating for enhanced protection.
Each coating level offers different degrees of protection, making it essential to choose the right grade for the application. Thicker coatings provide greater corrosion resistance, but processing methods play a crucial role in edge quality.
Processing Methods and Their Effects on Edge Quality
When shaping galvanized sheet steel, the primary methods include laser cutting, punching, and stamping. Each method affects the zinc coating differently, which in turn impacts edge corrosion resistance.
• Laser Cutting: Laser cutting vaporizes zinc at the cut, exposing the raw steel edge. This exposed steel edge is highly susceptible to oxidation due to the lack of protective zinc coating.
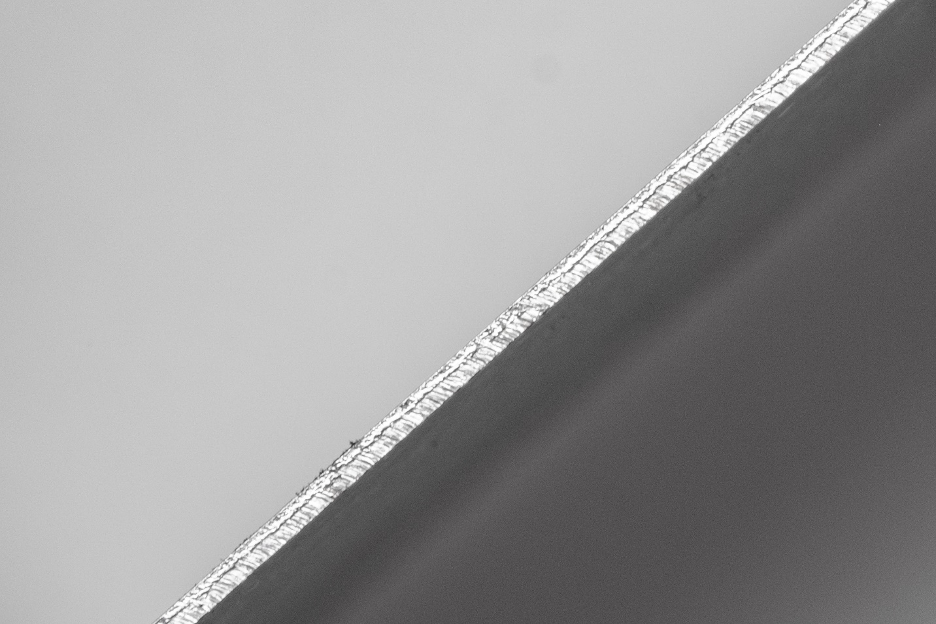
• Punching and Stamping: These methods shear the material, which often pulls some zinc from the sheet surface around the edge, creating a partial zinc layer. This residual zinc provides superior corrosion resistance compared to laser cutting by creating a sacrificial anodic layer.
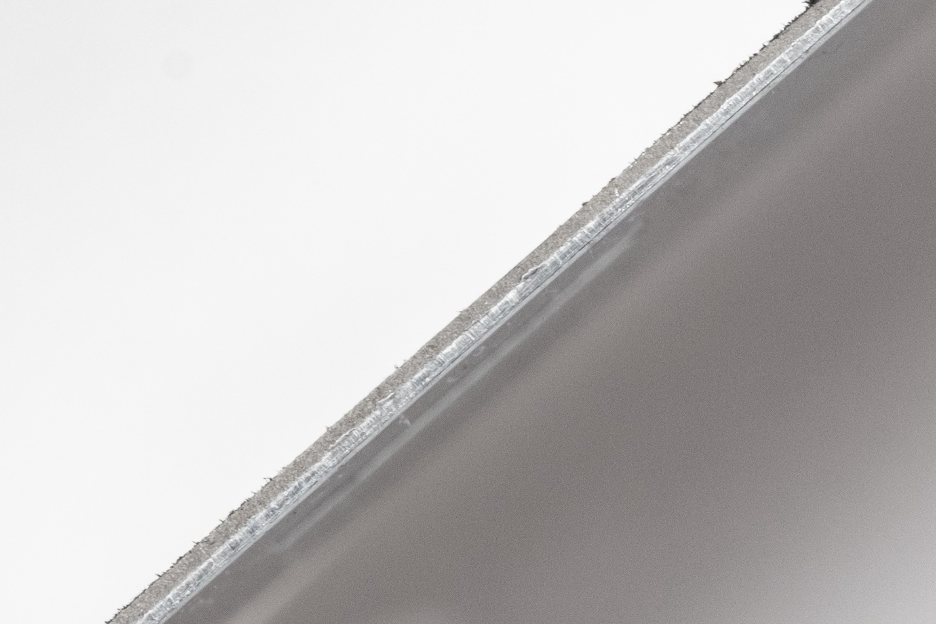
Enhancing Edge Protection with Roller Deburring
To further bolster corrosion resistance on punched edges, a roller ball deburring process can be applied. Roller deburring pushes any burrs back toward the cut edge, distributing the zinc coating more evenly across the edge. This technique not only enhances protection against corrosion but also smooths out sharp edges, improving safety and durability.
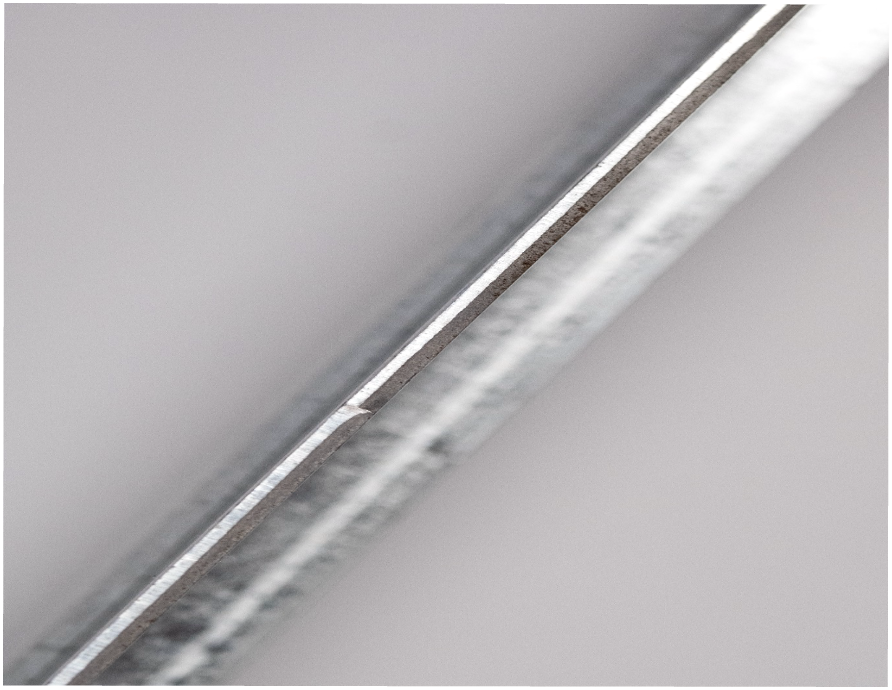
Choosing the Right Material Thickness for Optimal Edge Protection
Material thickness is another essential factor in galvanized sheet processing:
• Thinner materials (16 to 22 gauge) achieve the best edge corrosion resistance, especially when processed by punching followed by roller deburring.
• Thicker materials expose more of the raw steel at the edge, which increases susceptibility to oxidation and may require additional post-processing for adequate protection.
Process Considerations for Edge Quality
Selecting the proper fabrication method is critical to achieving the desired edge conditions:
• For thin materials where corrosion resistance is a priority, punching with roller deburring yields the best results.
• For thicker or laser-cut materials, applying a post-process zinc coating may be necessary to achieve optimal edge protection.
Enhancing Edge Protection with Roller Deburring
To further bolster corrosion resistance on punched edges, a roller ball deburring process can be applied. Roller deburring pushes any burrs back toward the cut edge, distributing the zinc coating more evenly across the edge. This technique not only enhances protection against corrosion but also smooths out sharp edges, improving safety and durability.
For a visual demonstration of the roller deburring process in action, you can view this video: Roller Ball Deburring Process Video.
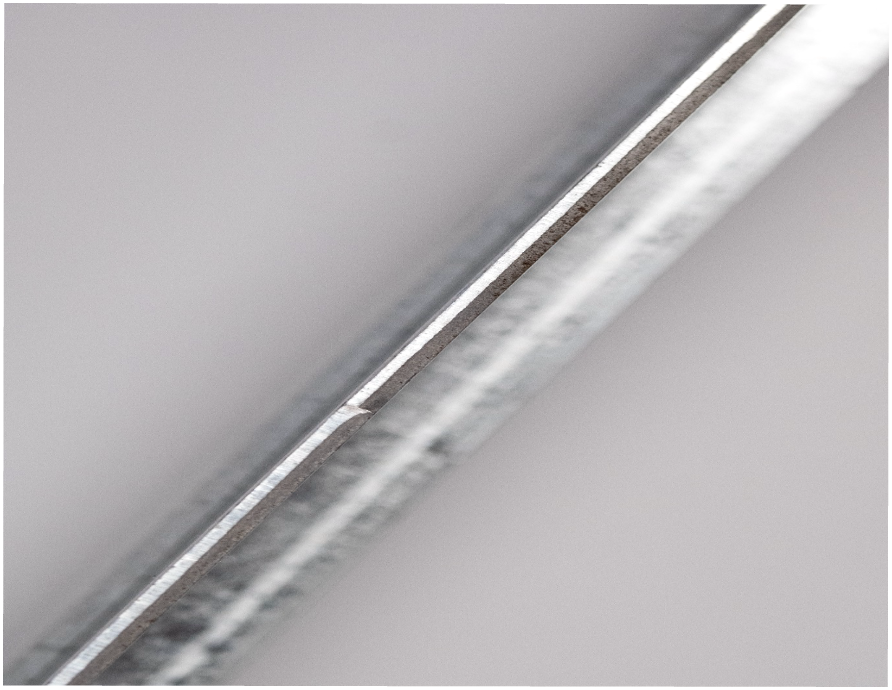
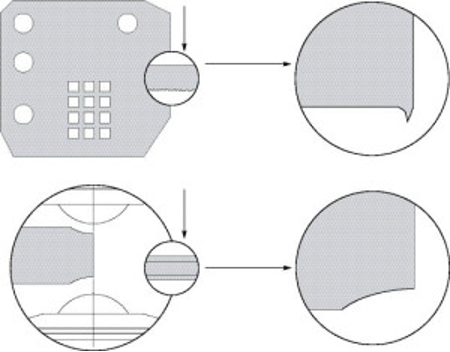
Testing Edge Quality in Humid Environments
Atlas conducted tests on cut and punched edges by placing parts in a humidity chamber at 85% relative humidity for 72 hours at 60°C. The results showed that punched edges with residual zinc protection displayed significantly higher corrosion resistance compared to laser-cut edges, which quickly showed signs of oxidation.
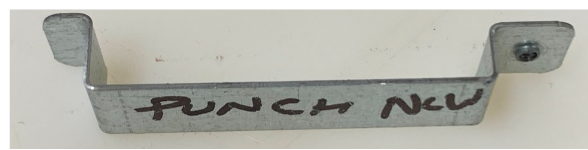
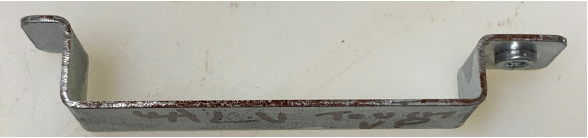
Conclusion
Understanding the effects of various processing methods on edge quality can greatly influence the durability of galvanized sheet steel components. Techniques like punching and roller deburring can enhance corrosion resistance by protecting edges, making these methods ideal for applications where longevity and quality are paramount. We encourage feedback on this Tech Talk and invite you to suggest topics for future editions, as we continue to share our expertise in metal fabrication.