What You’ll Learn About Welded Assemblies
- The types of welded joints used in precision sheet metal fabrication include butt joints, fillet welds, lap joints, and T-joints.
- Commonly used welding processes for assemblies are TIG welding, MIG welding, and spot welding.
- The importance of material selection in welded assemblies and its impact on the welding process.
Are welded assemblies the cornerstone of precision sheet metal fabrication? Welded assemblies are pivotal in precision sheet metal fabrication, forming the foundation of sturdy and intricately designed structures. Understanding the nuances of welded assemblies is crucial for fabricators and engineers aiming for superior quality and durability in their products.
Definition and Significance
In metalworking, welded assemblies refer to joining multiple metal components through the application of heat, pressure, or a combination of both. This method enables the creation of complex and robust structures, ensuring the structural integrity and longevity of the final products.
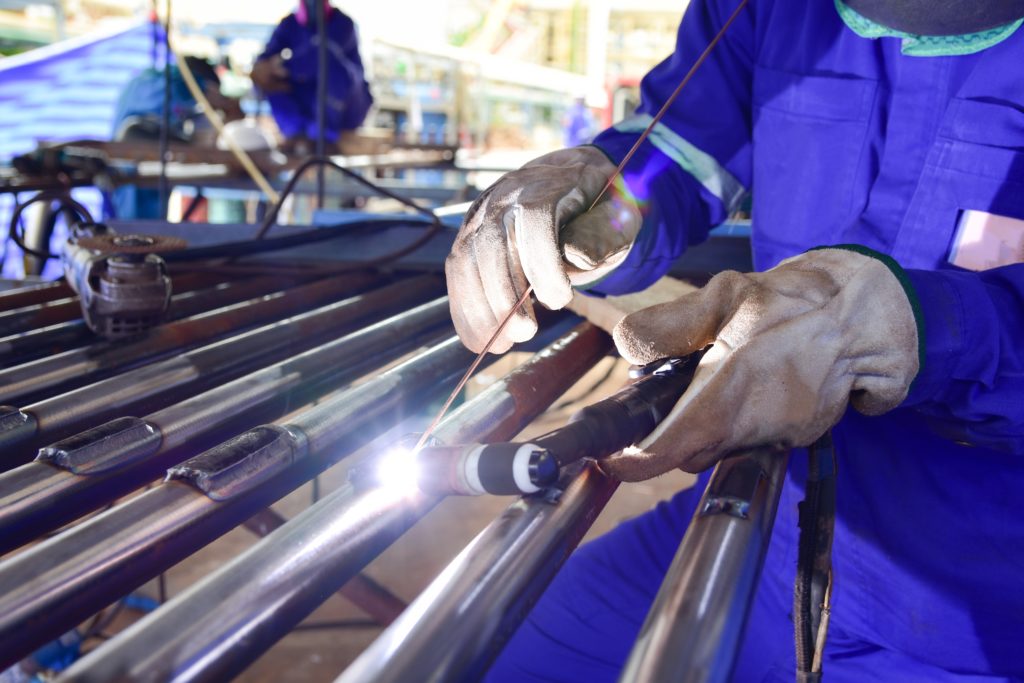
Role in Precision Sheet Metal Fabrication
Welded assemblies are indispensable for achieving the exacting standards of accuracy and strength demanded by various industries, from aerospace components to medical equipment, making them an integral part of the manufacturing landscape.
Understanding Welded Assemblies
Comprehending welded assemblies involves understanding the various joint types, welding processes, and material considerations that underpin their construction.
Types of Welded Joints
Butt Joints
Formed when two pieces of metal are aligned in the same plane and joined together along their edges. Common in structural welding where the appearance of the weld is crucial.
Fillet Welds
Triangular in cross-section and used to join perpendicular pieces of metal. Versatile and widely used due to their strength and ease of implementation.
Lap Joints
Involve overlapping the metal pieces and welding them together. Favored for its simplicity and suitability for joining different material thicknesses.
T-Joints
Formed when two metal pieces are joined at right angles, creating a T-shaped configuration. Common in structural and frame welding.
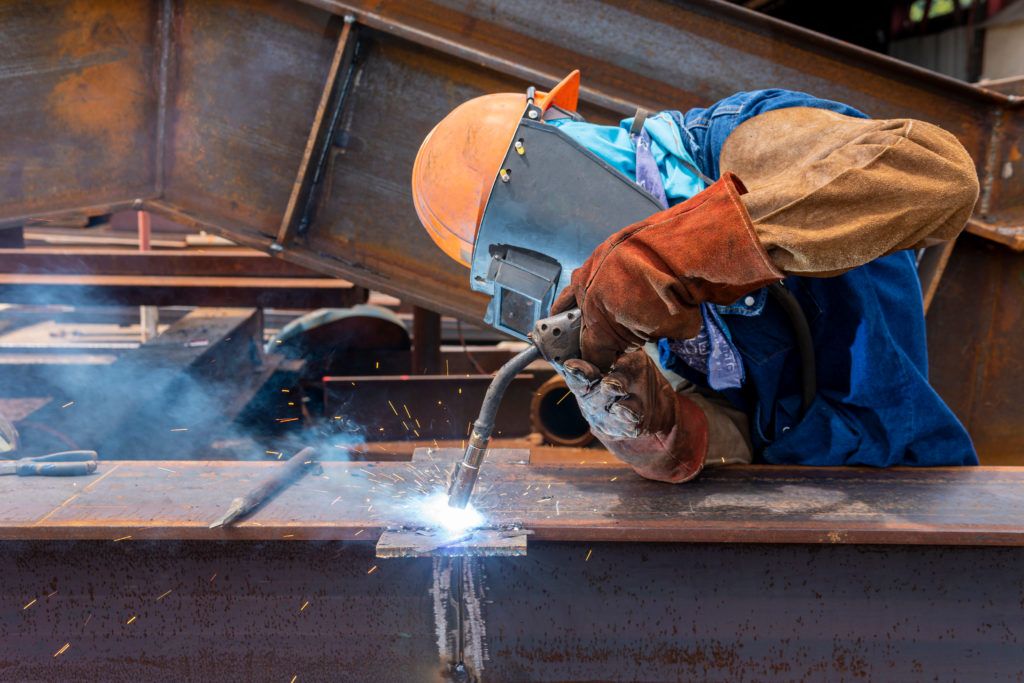
Commonly Used Welding Processes for Assemblies
TIG Welding
Precise and versatile welding process suitable for a wide range of metals, offering exceptional control over the welding arc and ideal for intricate and high-quality welds.
MIG Welding
Popular for its efficiency and ease of use, widely employed in industrial settings for producing strong and clean welds.
Spot Welding
A fast and economical method commonly used in automotive and electronic industries for its speed and cost-effectiveness.
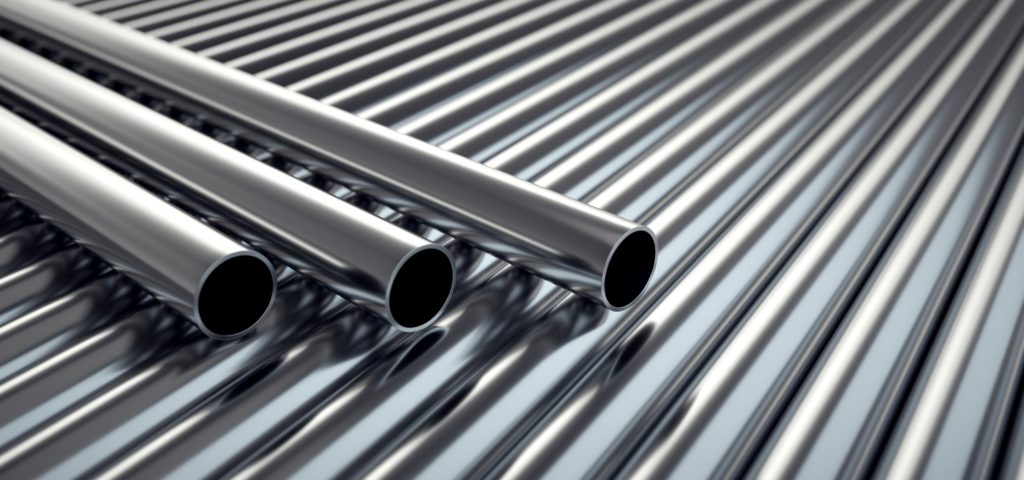
Importance of Material Selection in Welded Assemblies
The choice of material significantly impacts the welding process and the properties of the final welded assemblies, influencing factors such as material strength, thermal conductivity, and corrosion resistance.
Materials Used in Welded Assemblies
The materials utilized in welded assemblies range from stainless steel to aluminum, each offering distinct properties that influence the welding process and the performance of the final product.
Stainless Steel
Prized for its corrosion resistance and strength, making it a popular choice for welded assemblies in industries where hygiene and durability are paramount.
Aluminum
Favored for its lightweight nature and excellent conductivity, making it a go-to material for applications where weight reduction and heat dissipation are critical factors.
Carbon Steel
Widely used for structural and industrial purposes, offering exceptional strength and weldability.
Impact of Material Choice on Welding Process
The selection of the appropriate material is pivotal in ensuring the success of the welding process, as different materials demand specific welding techniques and considerations to achieve optimal results.
Welding Technique | Description | Common Applications |
---|---|---|
TIG Welding | Utilizes a non-consumable tungsten electrode and inert gas for precise and high-quality welds. | Aerospace components, automotive parts |
MIG Welding | Involves a continuous solid wire electrode and a shielding gas for efficient and clean welds. | Industrial manufacturing, construction |
Spot Welding | Joins metal surfaces by applying pressure and heat to a small area, ideal for mass production. | Automotive industry, electronic component assembly |
Welding Techniques and Equipment
Efficient and precise welding necessitates the utilization of advanced equipment and the mastery of diverse welding techniques tailored to the specific requirements of the welded assemblies.
Welding Equipment and Tools
Welding equipment encompasses an array of tools such as welding machines, gas cylinders, electrodes, and protective gear, all essential for ensuring safety and precision during the welding process.
Welding Techniques for Precision Sheet Metal Fabrication
The unique demands of precision sheet metal fabrication call for specialized welding techniques, including pulse welding, laser welding, and resistance welding, each offering distinct advantages in terms of accuracy and efficiency.
Applications of Different Welding Techniques
The versatility of welding techniques enables their application across a spectrum of industries, showcasing their adaptability and indispensability in diverse fabrication processes.
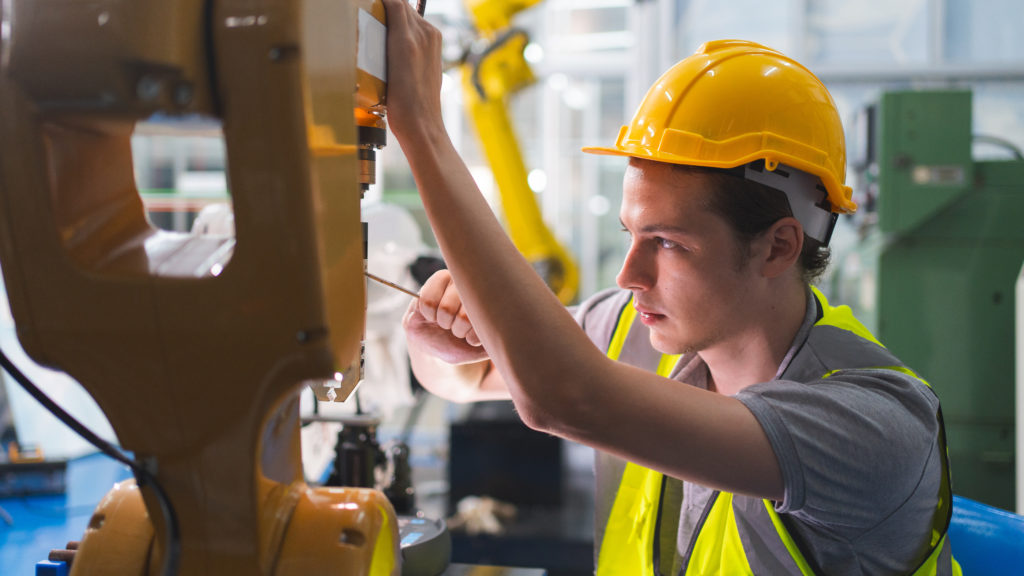
Quality Control and Inspection in Welded Assemblies
Ensuring the quality and integrity of welded assemblies is paramount in upholding safety standards and product reliability, necessitating rigorous inspection and adherence to industry benchmarks.
Importance of Quality Control in Welding
Quality control protocols encompass meticulous monitoring of weld integrity, dimensional accuracy, and material properties, safeguarding against defects and structural weaknesses in the assembled components.
Non-Destructive Testing (NDT) Methods
Non-destructive testing methods like ultrasonic testing, radiography, and magnetic particle inspection serve as indispensable tools for detecting internal flaws and irregularities in welded assemblies without compromising their structural integrity.
Standards for Ensuring Weld Integrity
Adherence to international standards and certifications, such as ISO 3834 for comprehensive quality requirements in welding, is instrumental in assuring the reliability and safety of welded assemblies across various industries.
Design and Fabrication of Welded Assemblies
The design and fabrication phase of welded assemblies demands meticulous planning and attention to detail to achieve optimal structural integrity and functionality.
Joint Design Considerations
Efficient joint design involves meticulous consideration of factors such as load-bearing requirements, stress distribution, and accessibility for welding, ensuring the robustness of the welded structure.
Fixture Design and Setup
The design of fixtures and jigs plays a pivotal role in stabilizing the components during welding, facilitating precise alignment and minimizing distortion, thereby enhancing the quality of the welded assemblies.
Material Thickness and Welding Considerations
The thickness of the material and the welding process are intricately linked, with thicker materials necessitating adjustments in welding parameters and techniques to attain strong and defect-free welded joints.
Advantages and Limitations of Welded Assemblies
The prevalence of welded assemblies is underpinned by their array of benefits, alongside inherent limitations and challenges that warrant careful consideration.
Strength and Durability of Welded Assemblies
Welded assemblies exhibit exceptional strength and durability, enabling the construction of robust and long-lasting structures that withstand rigorous operational demands, making them indispensable in critical applications.
Limitations and Challenges in Welding Processes
Challenges such as distortion, residual stress, and weld discontinuities pose inherent limitations in welding, necessitating the implementation of advanced techniques and meticulous control measures to mitigate these factors.
Industry Best Practices for Welded Assemblies
Adhering to industry best practices is paramount for achieving high precision and efficiency in welded assemblies, while ensuring compliance with stringent regulations and quality standards.
Tips for High Precision and Efficiency in Welding
Implementing meticulous welding procedures, optimizing welding parameters, and prioritizing operator training are pivotal for upholding precision and efficiency in welded assemblies, fostering superior quality and productivity.
Compliance with Industry Standards and Regulations
Adherence to industry-specific standards, such as ASME Boiler and Pressure Vessel Code for pressure vessel welding, is critical in ensuring the safety, reliability, and regulatory compliance of welded assemblies in various industrial sectors.
Case Studies and Applications of Welded Assemblies
Real-life case studies exemplify the diverse applications and benefits of welded assemblies across a spectrum of industries, shedding light on their pivotal role in enabling innovative and resilient engineering solutions.
Real-life Examples in Various Industries
From the construction of complex aerospace structures to the fabrication of intricate medical devices, welded assemblies serve as the linchpin of numerous applications, showcasing their versatility and indispensability in modern manufacturing.
Applications and Benefits Showcased
The applications of welded assemblies extend across industries, delivering benefits such as enhanced structural integrity, weight reduction, and manufacturing cost efficiencies, underscoring their multifaceted contributions to diverse engineering endeavors.

Future Trends and Innovations in Welded Assemblies
The trajectory of welded assemblies is poised for groundbreaking advancements, driven by emerging technologies and the integration of automation and robotics into welding processes.
Emerging Technologies in Welding
Cutting-edge technologies, including friction stir welding and laser-hybrid welding, are revolutionizing the landscape of welded assemblies, offering unprecedented precision, speed, and versatility in metal joining applications.
Automation and Robotics in Welding Processes
The integration of robotics and automation is poised to elevate the efficiency and consistency of welded assemblies, transforming manufacturing processes and unlocking new frontiers of productivity and quality in metal fabrication.
By delving into the intricacies of welded assemblies, fabricators and engineers can harness the full potential of these techniques to create durable, high-quality products across a range of industries.
Questions
What are precision sheet metal fabricated welded assemblies?
Precision sheet metal welded assemblies are products made by joining metal parts through welding, ensuring high accuracy and quality.
Who can benefit from using precision sheet metal welded assemblies?
Industries such as automotive, aerospace, electronics, and medical equipment can benefit from the use of precision sheet metal welded assemblies.
How are precision sheet metal welded assemblies manufactured?
These assemblies are manufactured using advanced techniques like laser welding, TIG welding, and robotic welding to ensure precision and strength.
What makes precision sheet metal welded assemblies superior?
Precision sheet metal welded assemblies offer superior strength, durability, and precise fabrication, making them ideal for demanding applications.
How can precision sheet metal welded assemblies streamline production?
By using automated welding processes, precision sheet metal welded assemblies can streamline production, reducing lead times and ensuring consistency.
What if my project requires custom precision sheet metal welded assemblies?
Many precision sheet metal fabrication companies offer custom solutions to meet specific project requirements, ensuring tailored welded assemblies.