What You’ll Learn About Electrical Enclosure Manufacturers
- Importance of electrical enclosures and manufacturers in precision sheet metal fabrication.
- Factors to consider when choosing electrical enclosure manufacturers.
- Material selection, design capabilities, and industry trends in electrical enclosure manufacturing.
Manufacturer | Customization Capabilities | Material Expertise | Industry Certifications | Customer Satisfaction |
---|---|---|---|---|
Manufacturer A | High | Stainless Steel, Aluminum | UL, NEMA, IP | Positive |
Manufacturer B | Moderate | Galvanized Steel, Aluminum | NEMA, IP | Mixed |
Manufacturer C | High | Stainless Steel, Galvanized Steel | UL, NEMA | Positive |
Manufacturer D | Moderate | Aluminum | NEMA, IP | Positive |
Manufacturer E | High | Stainless Steel, Aluminum | UL, NEMA, IP | Positive |
What are Electrical Enclosures and Why Are Electrical Enclosure Manufacturers Important?
Electrical enclosures are vital protective structures designed to safeguard electronic equipment from environmental factors such as dust, water, and extreme temperatures. As the reliance on electronic systems grows across various industries, the demand for reliable electrical enclosures continues to rise. Electrical enclosure manufacturers play a crucial role in precision sheet metal fabrication, specializing in crafting enclosures that adhere to stringent industry standards and cater to diverse industrial needs.
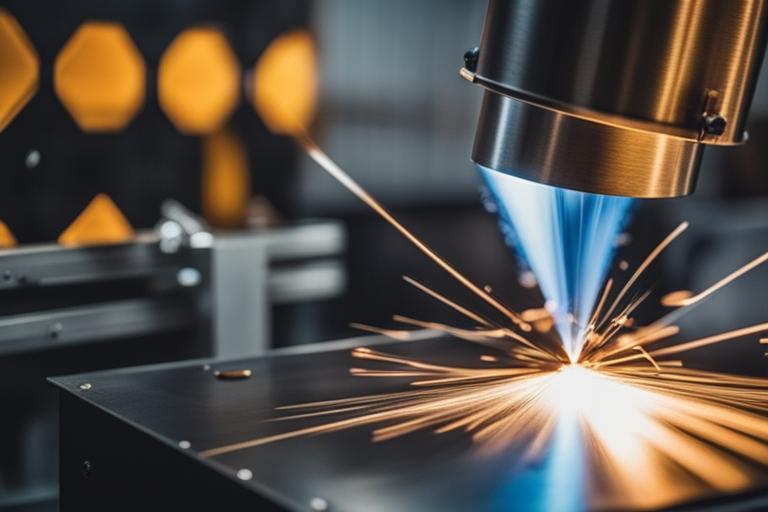
The Role of Electrical Enclosure Manufacturers in Precision Sheet Metal Fabrication
Electrical enclosure manufacturers utilize advanced fabrication techniques to create custom enclosures that meet specific requirements, ensuring the utmost protection for electronic equipment. They play a pivotal role in ensuring the quality, reliability, and compliance of enclosures with industry standards, ultimately contributing to long-term cost savings and enhanced operational efficiency.
Understanding Precision Sheet Metal Fabrication
The Significance of Precision Sheet Metal Fabrication in Electrical Enclosure Manufacturing
Precision sheet metal fabrication involves the cutting, bending, and assembling of sheet metal to create intricate and durable electrical enclosures. This process requires advanced machinery and skilled craftsmanship to produce enclosures that meet exact specifications and performance standards. It plays a crucial role in diverse industries, including telecommunications, renewable energy, industrial automation, and transportation, ensuring that electronic equipment remains protected in demanding operational environments.
Challenges and Requirements in Producing Electrical Enclosures
Fabricating electrical enclosures presents unique challenges, including achieving precise tolerances, selecting appropriate materials, and meeting industry-specific regulations. Manufacturers must also consider factors such as thermal management, corrosion resistance, and electromagnetic shielding to deliver enclosures that excel in diverse applications.
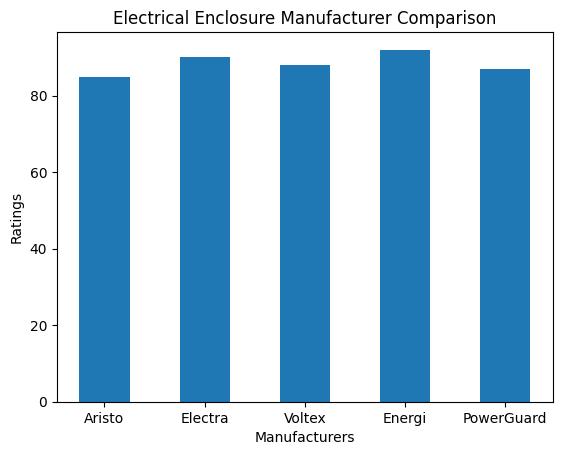
Factors to Consider When Choosing Electrical Enclosure Manufacturers
Key Considerations for Choosing Electrical Enclosure Manufacturers
When evaluating electrical enclosure manufacturers, key factors such as material quality and selection, customization capabilities, adherence to industry standards and certifications, and production capacity and lead times are pivotal. Leading manufacturers offer enclosures fabricated from high-grade metals such as stainless steel, aluminum, and galvanized steel, ensuring durability and protection against environmental stressors. The ability to provide customization and design flexibility is essential for meeting the unique requirements of different industries, and compliance with industry standards ensures the necessary protection and performance characteristics for their intended applications.
Customization and Design Capabilities of Electrical Enclosure Manufacturers
The Importance of Customization and Design in Electrical Enclosure Manufacturing
Tailored designs ensure that the enclosures seamlessly integrate with specific equipment and operational environments, optimizing functionality and performance. Leading electrical enclosure manufacturers offer advanced design capabilities and prototyping services to bring custom enclosure concepts to fruition, enabling clients to visualize and refine enclosure designs before full-scale production.
Utilization of CAD/CAM Software for Customization and Design
The utilization of Computer-Aided Design (CAD) and Computer-Aided Manufacturing (CAM) software empowers manufacturers to create intricate enclosure designs with exceptional precision. This technology facilitates the seamless translation of design concepts into manufacturable enclosures, enhancing efficiency and accuracy.
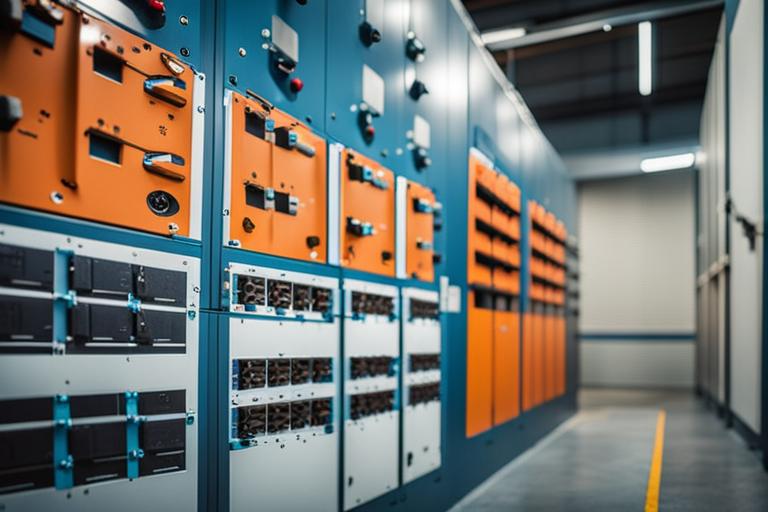
Quality Control, Compliance, and Testing
Ensuring Quality and Compliance in Electrical Enclosure Manufacturing
Quality control measures are imperative in ensuring the reliability and performance of electrical enclosures. Compliance with industry standards and certifications such as UL (Underwriters Laboratories), NEMA (National Electrical Manufacturers Association), and IP (Ingress Protection) ratings is non-negotiable, signifying a commitment to producing enclosures that meet or exceed established performance and safety benchmarks.
Testing and Certifications for Electrical Enclosures
Thorough testing and certification processes validate the performance and durability of electrical enclosures. Manufacturers conduct tests for factors such as ingress protection, impact resistance, and environmental performance to ensure that their enclosures meet the demands of real-world operating conditions.
Material Selection and Manufacturing Techniques
Key Materials and Manufacturing Techniques in Electrical Enclosure Manufacturing
Stainless steel, aluminum, and galvanized steel are among the most commonly used materials in electrical enclosure manufacturing, offering unique properties catering to diverse application requirements. Manufacturers employ advanced manufacturing techniques such as laser cutting, CNC punching, welding, and powder coating to fabricate precision electrical enclosures, enabling the creation of intricate designs while ensuring structural integrity and surface finishes.
Sustainable Materials and Manufacturing Practices
In response to environmental concerns, the adoption of sustainable materials and manufacturing practices is gaining traction in electrical enclosure manufacturing. Manufacturers are increasingly exploring eco-friendly materials and energy-efficient processes to minimize their environmental footprint while delivering high-quality enclosures.
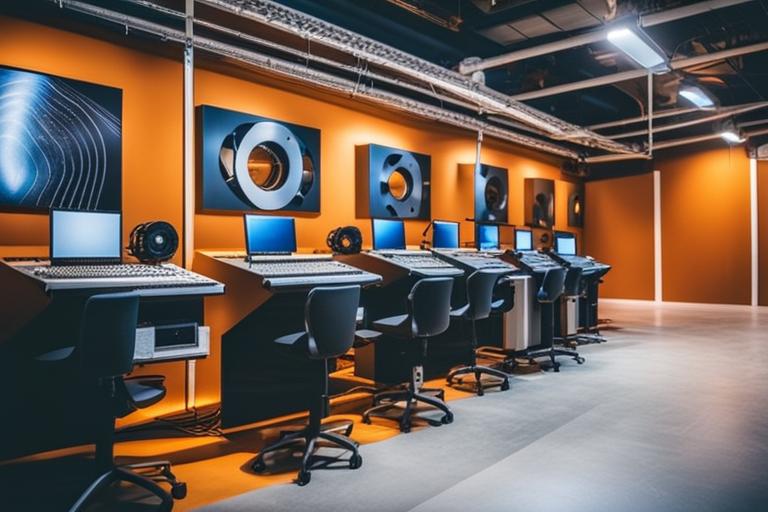
Industry Trends, Innovations, and Technology Integration
Latest Trends and Innovations in Electrical Enclosure Manufacturing
The electrical enclosure manufacturing industry is witnessing notable trends, including the rising demand for IoT (Internet of Things)-enabled enclosures, modular designs for scalability, and the integration of advanced materials for enhanced performance and longevity. The integration of smart technologies, such as IoT sensors and monitoring systems, is revolutionizing electrical enclosures, enabling real-time performance tracking, predictive maintenance, and enhanced operational insights.
Adaptation to Industry Shifts and Innovations
Manufacturers are adapting to industry shifts by embracing digitalization, automation, and data-driven decision-making processes. This adaptability allows manufacturers to stay at the forefront of technological advancements and deliver innovative solutions that align with evolving industry requirements.

Case Studies and Success Stories
Examples of Successful Partnerships with Electrical Enclosure Manufacturers
Several businesses have experienced successful partnerships with electrical enclosure manufacturers, resulting in tailored solutions that optimize equipment protection and operational efficiency. These collaborations demonstrate the tangible benefits of partnering with reputable manufacturers, highlighting their expertise in addressing complex enclosure requirements across various industries.
Impact of High-Quality Enclosures on Product Performance and Market Competitiveness
High-quality electrical enclosures have a direct impact on product performance and market competitiveness. Through case studies, businesses have illustrated how superior enclosures contribute to the reliability, safety, and longevity of their products, enhancing their competitive edge.
Illustrative Case Studies of Prominent Manufacturers and Their Contributions
Case studies featuring prominent manufacturers showcase their expertise in addressing complex enclosure requirements across various industries, providing insights into the capabilities and innovative approaches of leading manufacturers.
Choosing the Right Partner for Electrical Enclosure Manufacturing
Practical Guidance for Businesses in Selecting an Electrical Enclosure Manufacturer
Selecting the right partner for electrical enclosure manufacturing requires careful consideration of factors such as expertise, capabilities, and a track record of delivering high-quality solutions. Businesses should evaluate manufacturers based on their ability to meet specific project needs and industry standards.
Tips on Evaluating Potential Partners
When evaluating potential partners, businesses should assess factors such as design expertise, material knowledge, testing capabilities, and the ability to offer tailored solutions. An in-depth evaluation ensures that the chosen manufacturer aligns with the project’s technical and operational requirements.
Establishing Collaborative Relationships for Successful Project Outcomes
Collaborative relationships between businesses and electrical enclosure manufacturers foster transparent communication, innovative problem-solving, and the co-creation of solutions that precisely meet the needs of the end-users, contributing to successful project outcomes and long-term mutual success.
Comparison of Prominent Electrical Enclosure Manufacturers
Overview of Leading Electrical Enclosure Manufacturers
A comprehensive overview of leading electrical enclosure manufacturers provides businesses with valuable insights into the diverse capabilities and specialties offered by each manufacturer.
Comparative Analysis of Manufacturers Based on Key Factors
Conducting a comparative analysis based on key factors such as customization capabilities, material expertise, industry certifications, and customer satisfaction enables businesses to identify the manufacturer that best aligns with their specific requirements.
Customer Reviews and Satisfaction
Customer reviews and satisfaction ratings offer firsthand perspectives on the experiences of businesses that have partnered with electrical enclosure manufacturers, providing valuable reference points for businesses seeking to engage with reliable and reputable manufacturers.
Conclusion
Recap of Key Considerations in Choosing an Electrical Enclosure Manufacturer
Selecting the right electrical enclosure manufacturer involves careful consideration of factors such as material quality, design expertise, compliance with industry standards, and a track record of successful collaborations. By prioritizing these considerations, businesses can establish enduring partnerships with manufacturers that deliver exceptional value.
Future Outlook for Electrical Enclosure Manufacturing Industry
The future of the electrical enclosure manufacturing industry is poised for continued innovation, driven by the integration of smart technologies, sustainable practices, and adaptable design solutions, further enhancing the performance and reliability of electrical enclosures across diverse applications.
In conclusion, the selection of the right electrical enclosure manufacturer is essential for ensuring the protection and longevity of electronic equipment in various industrial applications, and businesses can benefit greatly from informed decision-making when choosing their manufacturing partners.
Frequently Asked Questions
Q: Who are some top electrical enclosure manufacturers?
A: Some top manufacturers include Hoffman, Hammond, and Rittal.
Q: What does precision sheet metal fabrication entail?
A: Precision sheet metal fabrication involves cutting, bending, and assembling sheet metal to create precise and complex parts.
Q: How are electrical enclosures fabricated with precision?
A: Electrical enclosures are fabricated with precision through advanced CNC machining and accurate assembly techniques.
Q: What if I need a custom electrical enclosure design?
A: Many manufacturers offer custom design services to meet specific requirements and dimensions.
Q: How can I ensure the quality of electrical enclosures?
A: You can ensure quality by choosing manufacturers with ISO certifications and a proven track record in the industry.
Q: What sets precision sheet metal fabrication apart?
A: Precision sheet metal fabrication sets itself apart through its ability to create intricate and accurate components for various industries.